Understanding CNC Machines
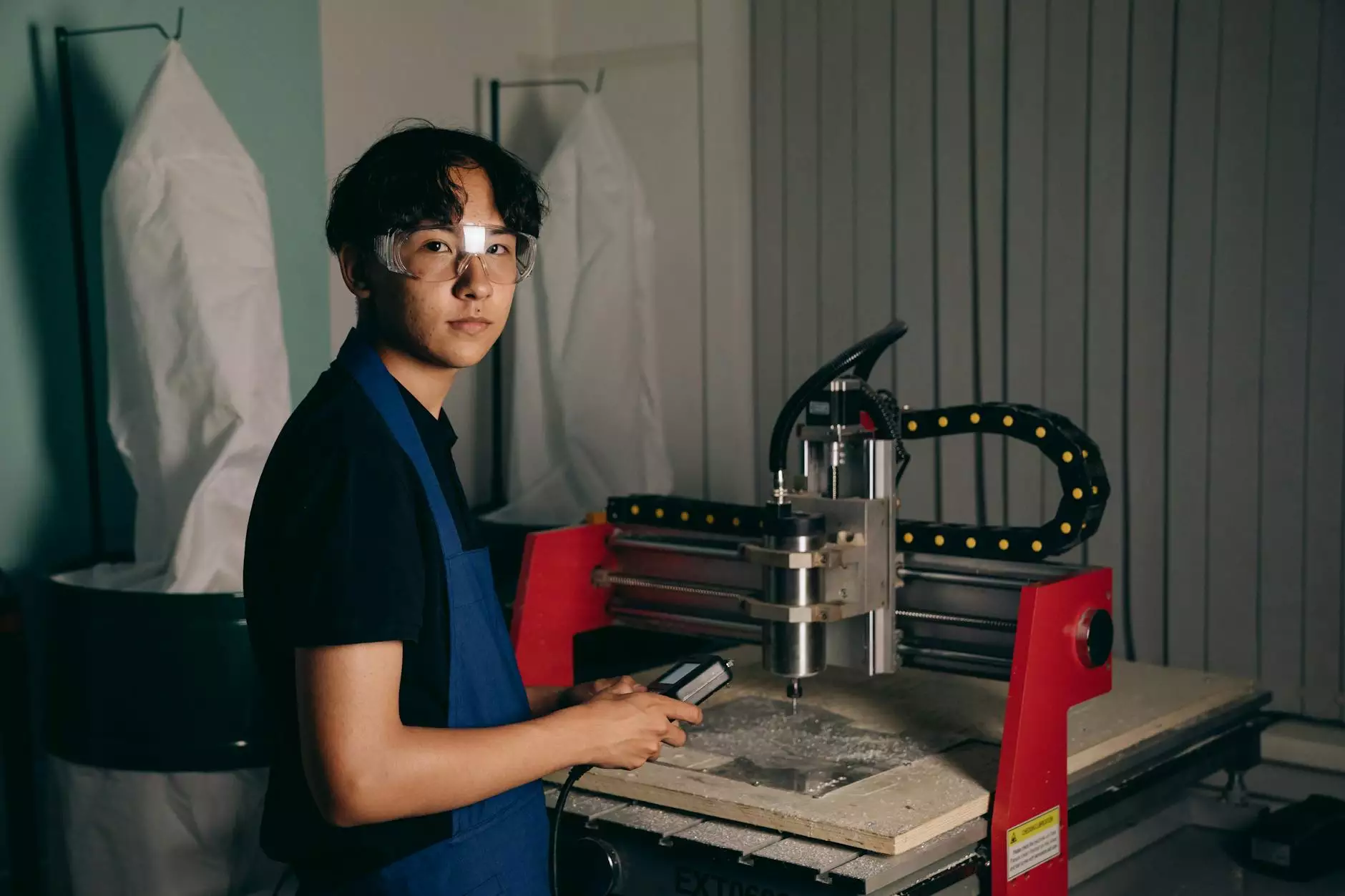
CNC machines are automated tools that have revolutionized the manufacturing industry with their unique ability to produce complex parts with incredible precision and consistency. Unlike traditional manufacturing methods that relied on manual operation through handwheels and levers, CNC machining leverages advanced technology and automation to enhance efficiency and productivity.
What is CNC Machining?
CNC machining stands for Computer Numerical Control machining, which refers to the automated control of machining tools (like drills, grinders, lathes, and mills) by means of a computer. In essence, it means that the operation of these machines is executed through pre-programmed software, ensuring a flawless manufacturing process.
The Evolution of CNC Machines
The journey of CNC machines began in the late 1940s and early 1950s, born out of the need for increased production efficiency within the manufacturing sector. Traditional machining methods were time-consuming and human error-prone. The introduction of numerical control (NC) systems marked a significant transition, allowing for better accuracy and repeatability in the production of components.
The Shift to Computer Control
The real breakthrough came when computers were introduced to run these NC systems, transforming them into what we now recognize as CNC machines. With the integration of computers, manufacturers could utilize G-code, a unique programming language that allows for precise control of machine tools.
How CNC Machines Work
Understanding how CNC machines operate involves grasping the key components and processes that make them effective:
Key Components of CNC Machines
- Controller: This is the brain of the CNC machine that interprets the G-code and sends signals to the motors and drives.
- Drive Motors: These motors move the machine's components, such as spinning the spindle and moving the tool or workpiece along the axes.
- Cutting Tools: These are necessary for shaping the material. They can be customized based on the material and the desired outcome.
- Workpiece: The raw material that is machined; it can be metal, plastic, or wood.
- Feedback Sensors: These ensure that the machine operates within specified tolerances by providing real-time data to the controller.
CNC Programming: The Role of G-code
CNC programming is essential in the operation of these machines, where G-code serves as the primary programming language. Essentially, G-code consists of a series of instructions that tell the machine how to perform specific operations, such as:
- Movement along different axes (X, Y, Z)
- Controlling spindle speed
- Setting feed rates
- Executing complex machining operations such as drilling, milling, and turning
The Importance of CAD and CAM
Alongside G-code, Computer-Aided Design (CAD) and Computer-Aided Manufacturing (CAM) software play crucial roles in the CNC machining process.
What is CAD?
CAD software is used to create precise drawings and specifications for the components to be manufactured. Designers can visualize and modify their designs in a digital environment, which enhances creativity and reduces material waste.
What is CAM?
Following the design phase, CAM software converts these CAD drawings into machinable instructions. It processes the design into commands that the CNC machine can understand, ensuring that every detail is meticulously accounted for in the production stage.
Types of CNC Machines
There exists a diverse array of CNC machine types, each tailored for specific applications:
1. CNC Milling Machines
CNC milling machines are versatile tools capable of performing a variety of milling and drilling tasks. They use rotary cutters to remove material from a workpiece, enabling complex shapes and features to be crafted.
2. CNC Lathes
Lathes are primarily used for turning operations. A workpiece is rotated against a cutting tool, which shapes the material through various angles and contours.
3. CNC Plasma Cutters
Ideal for cutting metals, CNC plasma cutters use assistive gases and a high-temperature plasma arc to pierce through materials, allowing for intricate designs and fast cutting speeds.
4. CNC Laser Cutters
Using focused laser beams, these machines can cut through various materials with high precision, making them perfect for industries requiring detailed designs and fine finishes.
5. CNC Waterjet Cutters
CNC waterjet cutters use high-pressure water jets mixed with abrasives to cut through tough materials without creating heat-affected zones, making it ideal for sensitive applications.
The Advantages of CNC Machining
CNC machining offers numerous benefits that have made it a staple in modern manufacturing:
- Precision: CNC machines can produce components with an accuracy often measured in micrometers, reducing errors and the need for post-production adjustments.
- Consistency: Once programmed, CNC machines can replicate the same component countless times without variation, ensuring uniform quality.
- Automation: CNC machining reduces labor costs and human error, as one skilled operator can oversee multiple machines simultaneously.
- Flexibility: Quick changes to designs can be made through software adjustments without the need for extensive retooling or downtime.
- Safety: As CNC machines operate autonomously, they minimize human interaction with potentially dangerous tools.
Challenges and Considerations in CNC Machining
Despite the advantages, there are challenges associated with CNC machining that manufacturers must address:
1. Initial Costs
Investing in CNC machines and software can be expensive. However, the long-term savings often justify the upfront investment.
2. Maintenance Requirements
Regular maintenance is essential to keep CNC machines running optimally. Downtime for repairs can affect production schedules.
3. Skill Shortage
Qualified CNC machinists and programmers are in high demand. Additional training and education are necessary to build a proficient workforce.
The Future of CNC Machining
The future of CNC machining continues to evolve with advancements in technology. The integration of Industry 4.0 concepts, including IoT (Internet of Things) connectivity and AI (Artificial Intelligence), are paving the way for smarter, more efficient systems:
1. Smart Factories
CNC machines are increasingly becoming interconnected, allowing for real-time data reporting and analytics that can inform production schedules, maintenance needs, and tool life management.
2. Automation and Robotics
Robots are being integrated into CNC machining processes, enabling automation of material handling, quality inspection, and even tool changeovers, further enhancing efficiency and reducing labor costs.
3. 3D Printing Integration
The convergence of CNC machining and additive manufacturing is opening new avenues in production capabilities, allowing manufacturers to create intricate parts that leverage both subtractive and additive techniques.
Conclusion
In conclusion, understanding CNC machining provides insight into how modern manufacturing functions efficiently and effectively. With continuous advancements in technology, CNC machines are set to play an even larger role in the future of production. As industries evolve, the integration of CNC systems will undoubtedly lead to more innovative solutions, higher productivity, and remarkable precision in the manufacturing landscape.
Learn More
Interested in diving deeper into the world of CNC machines? For more information, you can visit Robocon CNC for resources and expert insights tailored to CNC manufacturing.